Welcome to “Ask Deb from QA,” a new column from MxD.
Every week, Deb from QA — with decades of experience on the factory floor — will answer your questions to demystify and explain the digital manufacturing industry.
Please submit your questions to debfromqa@mxdusa.org
Deb, I keep hearing about this term “digital twin” and I have no idea what it means. Can you explain?
Ah yes, digital twin! No, it’s not a sequel to that Arnold Schwarzenegger/Danny DeVito movie (I’m really dating myself).
But really, it’s both an abstract idea and one with quite a lot of day-to-day use. Practically speaking, using digital twin will enable you to make your process more efficient, more efficiently! And more efficiency usually means time saved and more money in your pocket. It also can minimize risk by playing out a scenario before making the change in real life. Think of it as a virtual dress rehearsal.
Basically, digital twin is the blurring of lines between the physical and cyber spaces. It’s having a virtual model of a product or a process.
Here’s an example. Say you’re making chicken noodle soup. You ask yourself: “I wonder what it’d taste like if I added paprika? Or maybe a dash of fresh thyme?” So you add the paprika and you taste it. Then you add the fresh thyme and you taste it. You note to yourself: “Paprika isn’t all that good, but fresh thyme makes a big difference.”
Now, say that before you even got out your ingredients to start cooking, your stovetop told you: “Paprika wouldn’t be good, but adding fresh thyme would be delicious” — all happening with artificial intelligence, and all happening in real-time, based on the soup the stovetop “tasted” last time you made it? That’s what is so mind-blowing about the possibilities of the digital twin concept.
Let’s go back to the world of manufacturing. Say I’ve got motors and conveyors controlled by a programmable logic controller, a PLC. I have it running at a certain speed, but I want to see what would happen if I sped it up or slowed it down. A digital twin can correlate to the physical equipment without you even firing it up, and you can virtually test any change to the process and see how it works, before pulling the trigger.
Simulation is an offline process. Humans are doing the measurements and plugging the data into the simulation. Digital twin is one step above that idea — it removes the human middleman from the process. The digital twin would communicate directly with the PLC.
What does this mean in the long run? Time saved = increased efficiency = money saved. One of my favorite sayings about our industry: Downtime is evil.
So why aren’t more manufacturers using digital twin? Right now, it’s very expensive. You need to have the right software, sensors, data network and cyber assets to talk to each other. That takes a lot of work, expertise and investment. I’d say maybe 5% of manufacturers are using digital twin in their process.
But the good news is that as capabilities go up, costs will go down. And in the coming years, you’ll see more and more manufacturers employing it.
Remember when everyone had their 56K phone modems, and upgrading to ethernet was super expensive? That’s where we’re at now with digital twin. Soon, it’ll become as commonplace as getting WiFi on a plane.
Assiduously assuring quality,
Deb
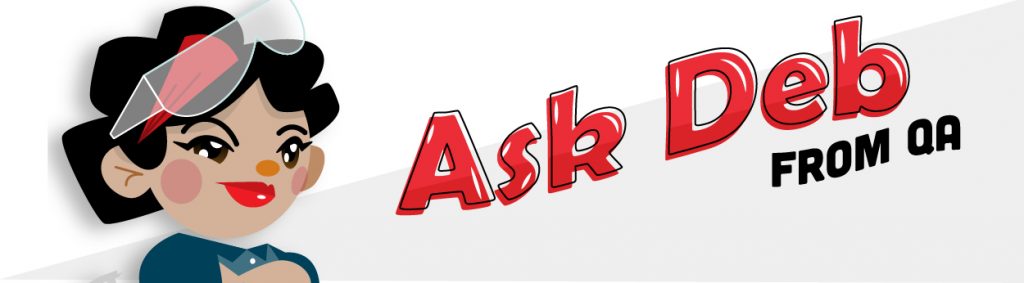
Deb from QA wants to hear your questions. Send ‘em to DebfromQA@mxdusa.org and she’ll answer as soon she gets off lunch.